Printed circuit boards (PCBs) provide connectivity foundations in electronics. Selecting flexible PCBs versus rigid PCBs constitutes an important design decision impacting device traits like durability, functionality and ergonomics. Analyzing distinctions in their attributes facilitates matching each PCB variety with ideal use cases.
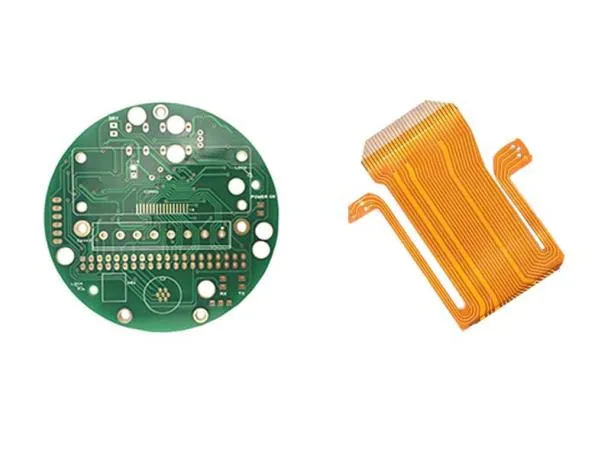
What Construction Defines Rigid PCBs?
Rigid PCBs utilize stiff, inflexible boards with copper traces etched or adhered onto substrate materials typically including paper-reinforced phenolic resins or glass-reinforced epoxy laminates. Benefits derived from rigidity encompass:
- Structural stability eases the operations in assembly processes
- Resists warping and maintains precise etch spacing in soldering procedures
- Simpler standard connectors accommodate rigidity
However, complete stiffness also imposes drawbacks:
- Lacks capacity to absorb dynamic mechanical strains
- Restricted potential configurations conforming to integrated package spaces
- Static bends during integration strain rigid PCB materials
The exclusive use of non-flexing board and component materials benefits rigidity in rigid PCBs when deployed in mechanically static applications without special ergonomic requirements.
What Properties Are Unique for Flexible PCBs?
Rather than glass fabric composites, flexible PCB fabrication utilizes pliable base materials like polyimide or polyester enabling moderate bending without fracturing traces or surface coatings. Additionally, flexible PCB components including cover layers and adhesives conform to continual mechanical agitation across expected movement ranges during device operation. Notable flexible PCB traits:
- Withstands repeated dynamic bending strains
- Enables wrapping circuits across multidimensional product contours
- Lightweight, thin form factors occupy minimal volume
- Demands special handling considerations during assembly
- Requires particularly reliable low-profile connections
In exchange for increased design and process complexity, flexible PCBs confer reliable mechanically dynamic characteristics vital for some applications.
How Do Manufacturing Processes Differ Between Flexible PCBs and Rigid PCBs?
Streamlined rigid PCB fabrication leverages the same fundamental substrate handling, imaging, etching, laminating and solder masking steps unchanged for decades, permitting widespread supply chain accessibility. By contrast, specialized flexible PCB process knowledge remains highly concentrated in dedicated manufacturers controlling niche chemistries and precision machining for reliably generating complex multilayer flex architectures. These barriers obstruct widespread flexible PCB supplies and contributing costs.
What Performance Factors Help Guide Appropriate Selection Between Flexible PCBs versus Rigid PCBs?
In static shear or compressive loading scenarios, rigid PCBs sustain greater power before material or connection failures. However, flexible PCB shows strong performance under continual dynamic mechanical cycling without crack propagation over timespans matching expected product lifetimes. Signal losses from transverse cable connections also exceed direct integrated transmission line losses in planar flexible PCBs.
Thermal management varies considerably. Rigid PCB substrates generally exhibit higher thermal conductivity than flexible counterparts, although metallic thermal spreader integration helps equalize capabilities.
How Do Application Spaces for Flexible PCBs and Rigid PCBs Align With Attributes?
Cost-sensitive digital logic applications without unusual size, weight or mechanical demands represent best spots for affordable, conventional rigid PCB fabrication techniques. By contrast, flexible PCB technology unlocks revolutionary form factor reduction and ergonomic shaping across consumer wearables, medical implants, defense aerospace systems and vehicular networking product categories where enabling capabilities outweigh manufacturing expenses.
Do Future Innovations Expand PCB Possibilities For Both Categories?
Ongoing research and development efforts promise exciting paradigm shifts on both rigid and flexible PCB fronts. Improved ceramic and liquid crystal polymer composite rigid PCB materials beat copper in thermal conductivity while retaining electrical isolation. Meanwhile, novel dynamic hybrid electronics integrate ultrathin flexible PCB materials able to coat additional substrates conformally , spanning structural electronics classes from prosthetics to autonomous robotics.
Yet balancing stiffness versus continual flexibility endures as a pivotal PCB selection consideration even under elevated performance limits, much as fundamental cost-against-capability trade-offs persist between Category 1 office printers and Category 6 industrial printers regardless of print resolution enhancements over time.
Does this flexible versus rigid PCB comparison help highlight key considerations in your PCB selection process? Please let me know if you would like any clarification or additional details on specific section topics as I would be happy to expand the discussion.