Flexible PCB
P/N: Q2E18851A0 | Layer Count: 1L | Min Line W/S: 16/8mil |
Material: Aluminum | Cu Thickness: 1oz | Min PTH: 0.2mm |
Board Thickness: 1 .0mm | Surface: OSP | Application:LED |
Soldermask Color: Yellow | Board Size: 289.00mmX265.00mm(20-up) |
Product Features
FPC (Flexible Circuit Board) is a type of PCB, also known as a "soft PCB". FPC is made of flexible substrates such as polyimide or polyester film, which has the advantages of high wiring density, light weight, thin thickness, flexibility, and high flexibility.
It is capable of withstanding millions of dynamic bends without damaging wires. FPC freely moves and expand according to spatial layout requirements, achieving three-dimensional assembly, achieving the integration of component assembly and wire connection, with advantages that the other types of circuit boards cannot match.
Option to Choose Flexible Material
Copper foil substrate includes electrolytic copper and rolled copper
A: Electrolytic copper foil substrate: refers to copper foil manufactured by electrolysis method. High ductility electrolytic copper foil: Flexibility higher than standard electrolytic copper foil, can be used together with standard electrolytic copper foil. Disadvantage: prone to cracking during bending, not suitable for dense lines
B: Rollyed copper foil substrate: It is made by repeatedly rolling copper blocks and then high-temperature tempering and toughening them. Its crystalline structure looks like sheet and has excellent softness, making it very suitable for making high-frequency, high-speed, fine and dense circuits. Advantages: Diffidult to Break, good bending resistence and high reliability.
Stack up of FPC
Here is one example of FPC. The structure of HDI combined with flex and rigid part, where resin plug holes and laser drilling in the hard rigid area are required.
Products application
-
Cosmic space
-
Automotive industry
-
Computers
-
Consumer Electronics
-
Telecommunications
-
Medical devices
Industry information
At present, the FPC production process is mainly divided into "sheet to sheet" and "roll to roll". The main raw material for producing FPC, FCCL, is provided in rolls. Under the "sheet to sheet" production process, the rolled FCCL needs to be cut into flakes before subsequent production can proceed, thus the efficiency of this process is relatively low; Under the "roll to roll" production process, the FCCL of the coils can be directly processed and produced. If this process reaches a stable state, it will greatly improve production efficiency and yield.
Overall, compared to developed countries abroad, China's FPC production capacity is still weak. There is still a certain gap in overall technical level compared to developed countries and regions such as Japan, the United States, and Taiwan. With the development of downstream mobile phones, computers, etc. towards miniaturization and lightweight, FPC is also developing towards high-density, ultra fine, and multi-layer directions.
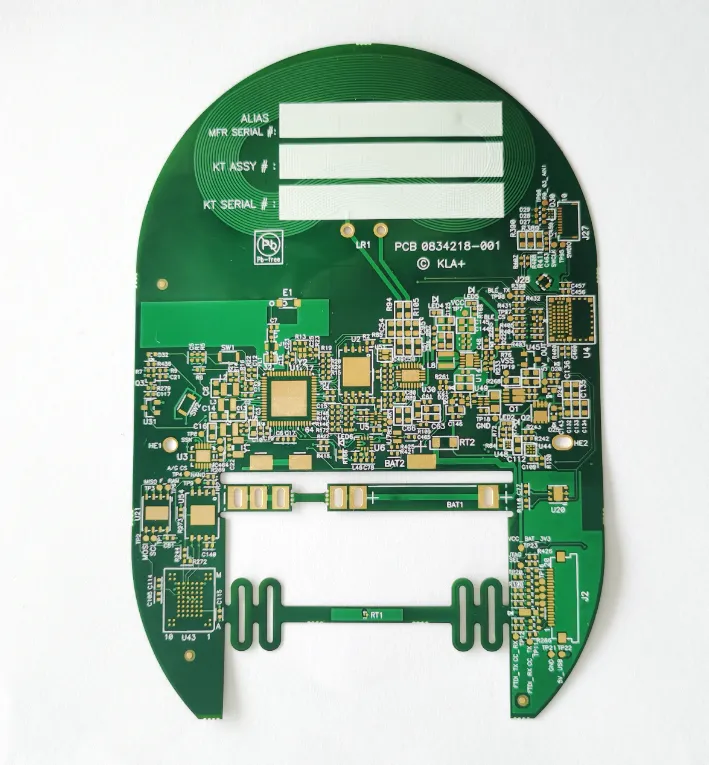
What is Flexible PCB?
Flexible Printed Circuit Boards (PCBs) are innovative electrical components designed to bend, twist, and fold without losing functionality. Unlike traditional rigid PCBs, these circuits are built on pliable substrates like polyimide or polyester, making them lightweight and adaptable. They’re trusted across industries for their ability to fit into tight spaces and withstand dynamic conditions, offering a reliable solution where rigidity just won’t do.
What Makes Up Flexible PCB Structure and Materials?
A flexible PCB isn’t just a single piece—it’s a carefully engineered stack of layers. The foundation is a flexible base material, typically polyimide, known for its heat resistance and durability. On top, thin copper foil forms the conductive pathways, while adhesive layers or bonding films hold it all together. A protective coverlay shields the circuits, ensuring they endure bending and environmental stress.
- Base Layer: Polyimide or polyester for flexibility.
- Conductor: Copper, etched into precise patterns.
- Coverlay: A protective film, often polyimide-based.
- Adhesives: Optional, for bonding layers securely.
How Do Flexible PCBs Work?
Flexible PCBs operate by conducting electrical signals through thin copper traces embedded in a bendable substrate. The magic lies in their ability to maintain connectivity even when flexed or shaped. The substrate insulates the circuits while the copper ensures efficient current flow. Their design allows them to handle dynamic movements—like in a folding phone—without cracking or shorting, thanks to the material’s elasticity and precise engineering.
Where Can Flexible PCBs Be Used?
Flexible PCBs shine in industries where space, weight, and adaptability matter. In consumer electronics, they power wearables like smartwatches and foldable screens. Medical devices rely on them for compact, reliable sensors that conform to the body. Aerospace and automotive sectors use them in tight, vibration-heavy environments, while robotics benefits from their ability to move with joints and limbs seamlessly.
- Wearables: Fitness trackers and smart clothing.
- Medical: Implantable devices and diagnostic tools.
- Automotive: Sensors in curved dashboards.
- Aerospace: Lightweight wiring in satellites.
How Are Flexible PCBs Designed and Made?
Creating a flexible PCB is a blend of precision design and advanced manufacturing. It starts with a concept and ends with a functional, bendable circuit. Here’s a step-by-step look at the process:
- Design Phase: Engineers use CAD software to map out the circuit layout, optimizing for flexibility and space.
- Material Selection: A flexible substrate like polyimide is chosen, paired with copper for conductivity.
- Etching: Copper is etched into patterns using photolithography, forming the circuit paths.
- Lamination: Layers are bonded together under heat and pressure.
- Finishing: A coverlay is applied, and the board is cut to shape, ready for testing.
This meticulous process ensures the final product meets both performance and flexibility demands.
Why Are Flexible PCBs Preferred Over Rigid PCBs?
Flexible PCBs stand out as a game-changer in electronics design, offering unique benefits that rigid PCBs can’t match. Here’s why they’re often the go-to choice:
- Adaptable Design: Flexible PCBs can bend and fold into tight or unconventional spaces, enabling sleeker, more innovative product designs like foldable gadgets or tiny medical devices.
- Enhanced Resilience: Built to endure vibrations, shocks, and flexing, they outlast rigid PCBs in demanding settings like vehicles or industrial machinery.
- Lightweight Build: Made with thinner, lighter materials, Flexible PCBs reduce the overall weight of devices—a crucial factor for wearables, aerospace, or handheld tech.
- Streamlined Assembly: By eliminating many connectors and cables, they simplify manufacturing and boost reliability by cutting down on weak points.
- Cost Savings in Complexity: For intricate, multi-layered designs, Flexible PCBs reduce production steps and material needs, making them economical for advanced applications.
These strengths position Flexible PCBs as a top pick for cutting-edge technology across multiple industries.
What Environments Suit Flexible PCBs Best?
Flexible PCBs thrive in diverse conditions, but their performance depends on how well their environment aligns with their properties. Key factors include:
- Extreme Temperatures: With materials like polyimide, they handle heat up to 200°C or cold down to -40°C, fitting applications from car engines to outdoor sensors.
- Moisture Levels: They resist humidity well with protective coatings, but in wet settings like marine or tropical areas, extra sealing is a must.
- Movement and Vibration: Perfect for dynamic uses—like fitness trackers or robotics—their flexibility shines, though bending limits must be respected.
- Chemical Presence: In factories or labs with corrosive substances, added shielding ensures they stay functional over time.
Tailoring their use to these conditions unlocks the full potential of Flexible PCBs in real-world scenarios.
How Do Manufacturers Test Flexible PCBs?
To guarantee Flexible PCBs meet high standards, manufacturers follow a step-by-step testing process. Here’s how it’s done:
- Step 1: Surface Check: Inspectors look for scratches, misaligned traces, or etching flaws using advanced magnifying tools.
- Step 2: Electrical Validation: Continuity checks confirm no broken paths, while isolation tests spot shorts that could disrupt performance.
- Step 3: Bend Testing: Boards undergo thousands of flex cycles to mimic real use, ensuring they won’t crack under stress.
- Step 4: Heat and Cold Trials: Thermal cycling exposes them to temperature swings, verifying stability in harsh climates.
- Step 5: Bonding Strength: Adhesion tests confirm that layers and traces stay intact even under strain.
Following standards like IPC-6013, these methods ensure every Flexible PCB is ready for its intended role.
How Is Quality Maintained in Flexible PCB Manufacturing?
Producing reliable Flexible PCBs demands precision at every stage. Here’s how quality is locked in:
- Top-Notch Materials: Using durable polyimide films and high-purity copper ensures flexibility without sacrificing conductivity.
- Accurate Etching: Cutting-edge photolithography crafts precise circuits, avoiding errors that could compromise function.
- Layer Precision: In multi-layer boards, exact alignment prevents signal issues or electrical faults.
- Automated Scans: Machines with optical inspection catch tiny defects—like incomplete traces—before they become problems.
- Thorough Final Checks: Electrical, mechanical, and environmental tests confirm each board meets strict specs.
This meticulous approach delivers Flexible PCBs that perform consistently, no matter the application.
What Steps Should You Take to Protect Flexible PCBs?
Flexible PCBs are tough, but proper handling keeps them in top shape. Consider these precautions:
- Limit Bending: Stick to the maker’s bend radius to avoid cracking delicate traces.
- Static Safety: Wear anti-static gear during installation to shield components from ESD damage.
- Stable Mounting: Secure them firmly to prevent flexing stress during use.
- Heat Caution: Avoid rapid temperature shifts to protect against layer separation.
- Waterproofing: Add coatings or cases in damp areas to block moisture damage.
Taking these steps ensures Flexible PCBs stay reliable and effective over the long haul.
FAQ
Reviews
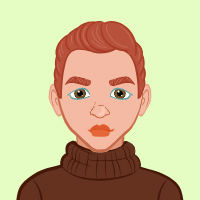
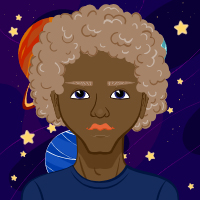
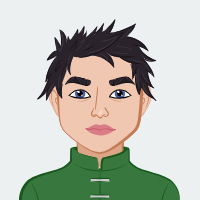
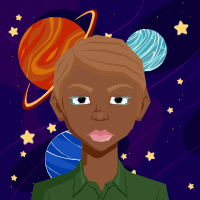
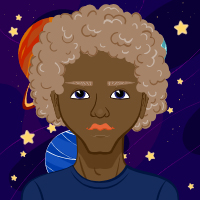
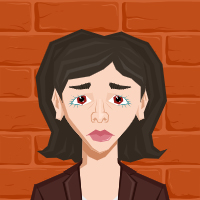
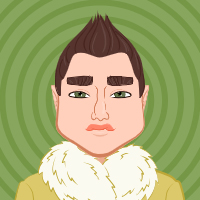
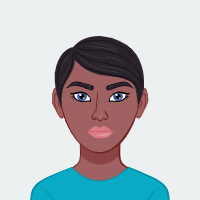
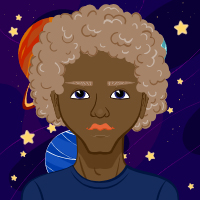
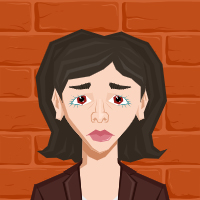