Rigid-Flex PCB
P/N: S4157946A0 | Layer Count: 4L | Min Line W/S: 16/8mil |
Material: GF212 TG130M | Cu Thickness: 1oz. | Min PTH: 0.45mm |
Board Thickness: 1. 6mm | Surface: AU2’’ | Application:industry control |
Soldermask Color: Green | Board Size: 130mm*110mm |
Product Features
What is Rigid-Flex PCB:
Rigid-Flex printed circuit boards are boards have both of flexible and rigid board feature. Most rigid flex boards consist of multiple layers of flexible circuit substrates attached to one or more rigid boards externally and/or internally, depending upon need of the application.
Rigid-Flex PCBs Fabrication Applications:
Rigid-flex PCB is widely used and has penetrated into all walks of life from daily consumer electronics. Due to its ability to save space and reduce weight, rigid-flexible board manufacturing is increasingly used in precision instruments such as pacemakers. The same advantages of using rigid-flex boards can also be applied to intelligent control systems. The rigid-flex combination not only maximizes space and weight (the flexible PCB part is particularly good at overcoming the space and weight issues of spatial freedom.), but also greatly improves reliability and eliminates most of the difficult-to-solve problems that arise during the production process. .
Rigid-flex board technology and production process:
The rigid-flex manufacturing stage is also more complex and time-consuming than rigid panel manufacturing. All flex components of rigid-flex components have completely different handling, etching and soldering processes than rigid FR4 boards
Whether producing rigid-flex prototypes or mass production of rigid-flex PCBs, fully proven and reliable technical requirements are required. Manufacturers should consider the feasibility of solutions from the early stages of the design phase and be involved in the entire product process from design to production to ensure that the design and manufacturing parts are coordinated and changes in the final product are taken into account.
Benefits of Rigid-Flex PCBs
• Simplifies the dependence on components between rigid components and reduces the weight of the entire circuit board.
• Reduced solder joints improve connection reliability.
• The assembly process is easier to handle than flexible circuit boards.
• Simplified PCB assembly process.
• Significantly reduced logistics and assembly costs.
Products application
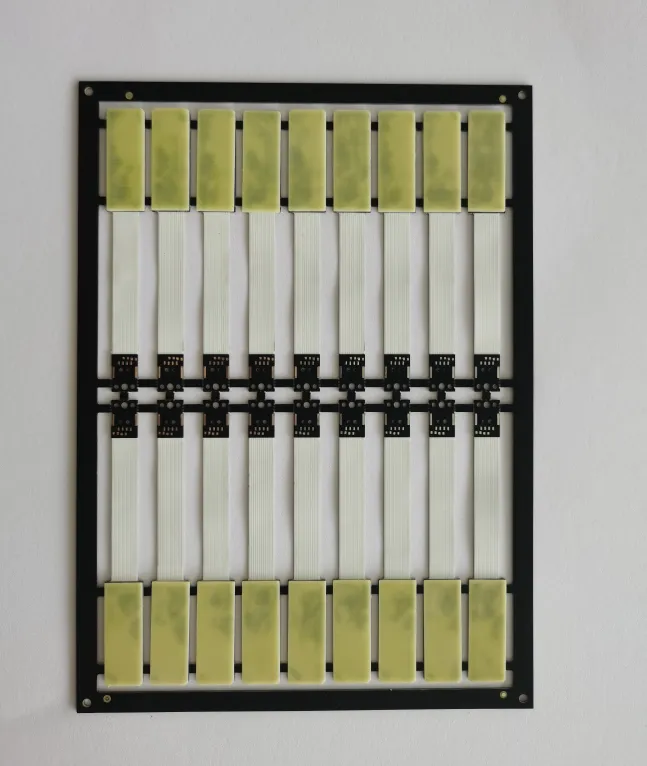
With the development and improvement of printed circuit technology, the development and research of rigid-flex boards have been widely used. It has become an inevitable trend for circuit boards to develop in the direction of being light, thin, short, small, and multi-functional, especially for high-density interconnect structures. The application of (HDI) rigid-flex boards will greatly promote the rapid development of circuit technology, and it is expected that the global supply of rigid-flex boards will increase significantly in the future. At the same time, the durability and flexibility of soft-hard composite boards make them more suitable for medical and military applications, gradually eroding the market share of rigid PCBs.
Although the product is good, the manufacturing threshold is somewhat high. Among all types of PCBs, soft and hard bonding boards have the strongest resistance to harsh application environments, making them favored by medical and military equipment manufacturers. Soft and hard bonding boards combine the durability of rigid PCBs with the adaptability of flexible PCBs. Enterprises in Chinese Mainland are increasing the proportion of such PCBs in the total output to take full advantage of the great opportunity of growing demand. Reducing the assembly size and weight of electronic products, avoiding wiring errors, increasing assembly flexibility, improving reliability, and achieving three-dimensional assembly under different assembly conditions is an inevitable demand for the growing development of electronic products. Flexible circuits, as an interconnection technology with thin, light, and flexible characteristics that can meet three-dimensional assembly needs, have been increasingly widely applied and valued in the electronics and communication industry.
Industry information
The following three boards are Rigid-Flex board which was made by us.
With the continuous expansion of its application fields, the technology of flexible circuit boards is also constantly developing, such as from single-sided flexible boards to double-sided, multi-layer, and even rigid flexible boards. The application of thin line width/spacing, surface installation and other technologies, such as the material characteristics of the flexible substrate itself, has put forward stricter requirements for the production of flexible boards, such as substrate treatment, interlayer alignment, control of dimensional stability, and decontamination, The reliability of small hole metallization, electroplating, and surface protective coating should be highly value.
What is a Rigid-Flex PCB?
A Rigid-Flex PCB is a hybrid circuit board that merges the benefits of rigid and flexible printed circuit boards into one cohesive design. It features rigid sections for stability and component mounting, combined with flexible areas that can bend or fold. This innovative structure allows it to adapt to tight spaces and complex layouts, offering a solution where traditional PCBs fall short. Widely used in industries like aerospace, medical, and consumer electronics, Rigid-Flex PCBs provide a reliable and space-saving option for modern devices.
How is a Rigid-Flex PCB Structured?
A Rigid-Flex PCB comprises alternating layers of rigid and flexible materials, typically bonded with adhesives or heat processes. The flexible portions are made from polyimide, a durable and bendable material, while the rigid sections use FR4 or similar substrates for strength. Electrical connections between layers are achieved through vias or plated through-holes. Designers strategically plan the placement of these sections, ensuring smooth transitions and optimal flexibility, which enhances the board’s ability to perform in compact or dynamic environments.
How Do Rigid-Flex PCBs Work?
Rigid-Flex PCBs function by transmitting electrical signals through conductive traces, much like standard PCBs, but with added flexibility. The rigid areas house components and provide structural support, while the flexible sections allow the board to bend without breaking the circuit. This design reduces reliance on external connectors, improving signal reliability and enabling the board to fit into unconventional shapes. It’s a seamless blend of stability and adaptability, tailored for applications requiring both durability and flexibility.
Where Are Rigid-Flex PCBs Used?
Rigid-Flex PCBs play a vital role in advanced electronics across multiple sectors. Here are some key applications:
- Aerospace: Enables lightweight, reliable circuits in satellites and avionics.
- Medical: Powers compact devices like hearing aids and diagnostic tools.
- Consumer Electronics: Supports foldable gadgets such as smartphones and smartwatches.
- Automotive: Enhances systems like sensors and dashboards with vibration resistance.
Their versatility makes them indispensable in technologies where performance and space constraints are critical.
How Are Rigid-Flex PCBs Designed and Manufactured?
The creation of a Rigid-Flex PCB involves a detailed process to balance flexibility and functionality. Here’s a step-by-step breakdown:
- Conceptual Design: Define rigid and flexible zones based on the device’s requirements.
- Material Prep: Select polyimide for flexibility and FR4 for rigidity.
- Circuit Layout: Etch conductive patterns using advanced imaging techniques.
- Lamination: Bond layers together under controlled heat and pressure.
- Finishing: Drill vias, plate connections, and test the final board.
This meticulous approach ensures the board meets both design specs and industry standards.
Why Choose Rigid-Flex PCBs Over Traditional PCBs?
Rigid-Flex PCBs offer distinct advantages that set them apart from conventional rigid or flexible boards:
- Compact Design: Folds into smaller spaces, ideal for miniaturized devices.
- Reliability: Fewer connections reduce failure risks.
- Lightweight: Cuts down on extra wiring and connectors.
- Performance: Shortens signal paths for better efficiency.
These benefits make them a top choice for cutting-edge applications needing both form and function.
What Conditions Are Ideal for Rigid-Flex PCBs?
Rigid-Flex PCBs thrive in diverse environments, but specific conditions maximize their performance:
- Temperature: Operates well between -40掳C and 150掳C, suitable for extreme settings.
- Movement: Flexible areas endure vibrations, perfect for mobile devices.
- Moisture: Benefits from protective coatings in humid conditions.
Adapting to these factors ensures their durability across aerospace, automotive, and beyond.
How Are Rigid-Flex PCBs Tested?
Testing Rigid-Flex PCBs ensures they meet high-quality standards through various methods:
- Visual Checks: Scans for physical flaws or misalignment.
- Electrical Tests: Confirms circuit integrity and connectivity.
- Bend Tests: Assesses flexibility under stress.
- Thermal Tests: Evaluates performance across temperature shifts.
These steps verify the board’s readiness for real-world challenges.
How Is Quality Ensured in Rigid-Flex PCB Production?
Quality assurance in Rigid-Flex PCB manufacturing involves rigorous oversight:
- Material Verification: Tests raw materials for consistency.
- Process Monitoring: Tracks each production stage for accuracy.
- Final Validation: Conducts functional tests to confirm specs.
This ensures every board delivers top-tier performance and reliability.
What Precautions Should Be Taken With Rigid-Flex PCBs?
Using Rigid-Flex PCBs requires care to maintain their integrity:
- Bend Limits: Avoid exceeding the designed flex radius.
- Static Control: Use ESD protection during handling.
- Heat Exposure: Keep within temperature tolerances.
These precautions safeguard their longevity and effectiveness.
FAQ
Reviews
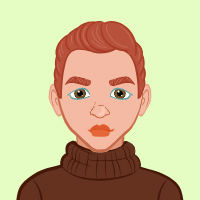
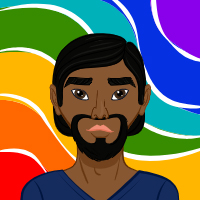
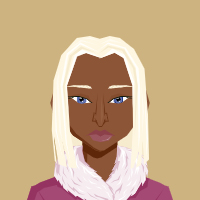

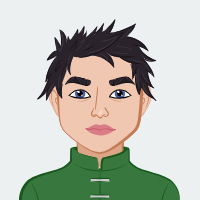
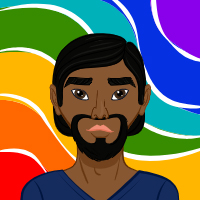
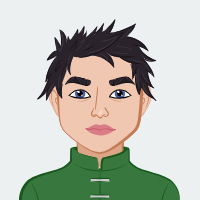
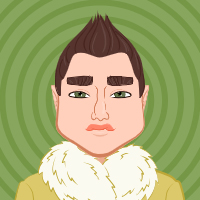
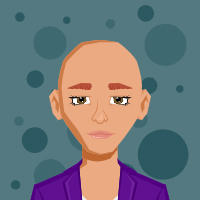
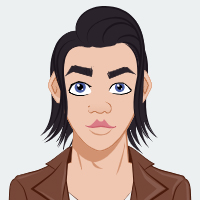