Flexible Leiterplatte
P/N: Q2E18851A0 | Anzahl der Schichten: 1L | Min. Linie W/S: 16/8mil |
Material: Aluminium | Cu Dicke: 1oz | Min. PTH: 0,2 mm |
Dicke der Platte: 1,0 mm | Oberfläche: OSP | Anwendung: LED |
Farbe der Lötmaske: Gelb | Platinengröße: 289,00 mm x 265,00 mm (20 up) |
Produktmerkmale
FPC (Flexible Leiterplatte)ist eine Art von Leiterplatte, die auch als "weiche Leiterplatte" bezeichnet wird. FPC besteht aus flexiblen Substraten wie Polyimid oder Polyesterfolie, die die Vorteile einer hohen Verdrahtungsdichte, eines geringen Gewichts, einer dünnen Dicke, einer hohen Flexibilität und einer hohen Flexibilität haben.
Es ist in der Lage, Millionen von dynamischen Biegungen standzuhalten, ohne Drähte zu beschädigen. FPC bewegt sich frei und erweitert sich entsprechend den Anforderungen der räumlichen Layout, erreicht eine dreidimensionale Montage und erreicht die Integration von Komponentenmontage und Drahtverbindung, mit Vorteilen, die die anderen Arten von Leiterplatten nicht bieten können.
Option zur Auswahl von flexiblem Material
Das Kupferfoliensubstrat umfasst elektrolytisches Kupfer und gewalztes Kupfer
A: Elektrolytisches Kupferfoliensubstrat: bezieht sich auf Kupferfolie, die durch Elektrolyseverfahren hergestellt wird. Elektrolytische Kupferfolie mit hoher Duktilität: Flexibilität höher als Standard-Elektrolyt-Kupferfolie, kann zusammen mit Standard-Elektrolyt-Kupferfolie verwendet werden. Nachteil: anfällig für Rissbildung beim Biegen, nicht geeignet für dichte Linien
B: Rollyed Kupferfoliensubstrat: Es wird hergestellt, indem Kupferblöcke wiederholt gewalzt und dann bei hohen Temperaturen gehärtet und gehärtet werden. Seine kristalline Struktur sieht aus wie Blech und hat eine ausgezeichnete Weichheit, wodurch es sich sehr gut für die Herstellung von Hochfrequenz-, Hochgeschwindigkeits-, feinen und dichten Schaltungen eignet. Vorteile: Schwer zu brechen, gute Biegefestigkeit und hohe Zuverlässigkeit.
Aufbau von FPC
Hier ist ein Beispiel für FPC. Die Struktur von HDI kombiniert mit flexiblen und starren Teilen, bei denen Harzstopfenlöcher und Laserbohren im harten starren Bereich erforderlich sind.
Anwendung der Produkte
-
Kosmischer Raum
-
Automobilindustrie
-
Computer
-
Unterhaltungselektronik
-
Telekommunikation
-
Medizinprodukte
Brancheninformationen
Gegenwärtig wird der FPC-Produktionsprozess hauptsächlich in "Blech zu Blech" und "Rolle zu Rolle" unterteilt. Der Hauptrohstoff für die Herstellung von FPC, FCCL, wird in Rollen bereitgestellt. Beim Produktionsprozess "Blech zu Blech" muss das gewalzte FCCL in Flocken geschnitten werden, bevor die nachfolgende Produktion fortgesetzt werden kann, daher ist die Effizienz dieses Prozesses relativ gering. Beim Produktionsprozess "Rolle zu Rolle" kann das FCCL der Coils direkt verarbeitet und hergestellt werden. Wenn dieser Prozess einen stabilen Zustand erreicht, wird er die Produktionseffizienz und -ausbeute erheblich verbessern.
Insgesamt ist Chinas FPC-Produktionskapazität im Vergleich zu den Industrieländern im Ausland immer noch schwach. Es gibt immer noch eine gewisse Lücke im technischen Gesamtniveau im Vergleich zu entwickelten Ländern und Regionen wie Japan, den Vereinigten Staaten und Taiwan. Mit der Entwicklung von nachgelagerten Mobiltelefonen, Computern usw. in Richtung Miniaturisierung und Leichtbau entwickelt sich FPC auch in Richtung hochdichte, ultrafeiner und mehrschichtiger Richtungen.
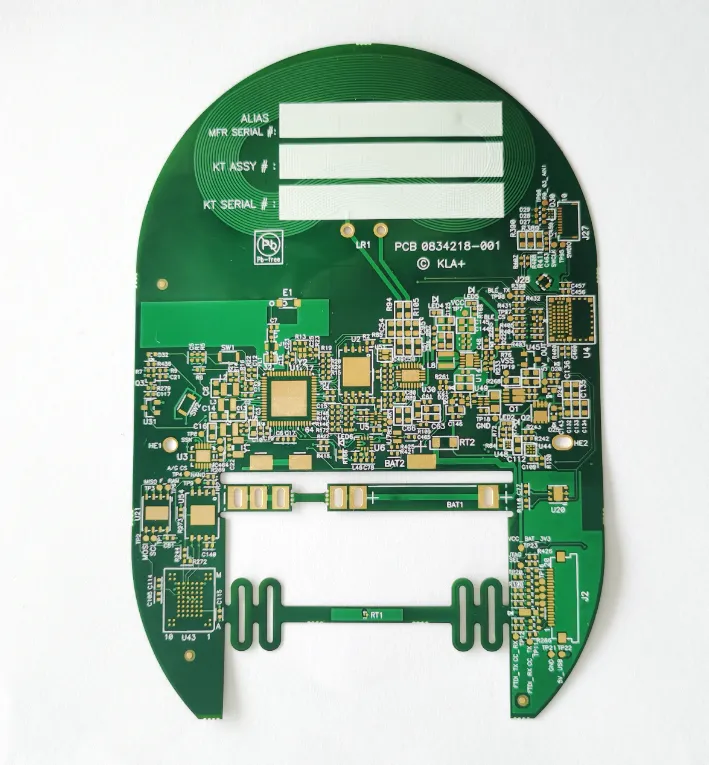
Was ist eine flexible Leiterplatte?
Flexible Leiterplatten (PCBs) sind innovative elektrische Komponenten, die sich biegen, verdrehen und falten lassen, ohne an Funktionalität zu verlieren. Im Gegensatz zu herkömmlichen starren Leiterplatten sind diese Schaltkreise auf biegsamen Substraten wie Polyimid oder Polyester aufgebaut, was sie leicht und anpassungsfähig macht. Sie werden in allen Branchen für ihre Fähigkeit geschätzt, in enge Räume zu passen und dynamischen Bedingungen standzuhalten, und bieten eine zuverlässige Lösung, bei der Steifigkeit einfach nicht ausreicht.
Was macht flexible Leiterplattenstruktur und -materialien aus?
Eine flexible Leiterplatte besteht nicht nur aus einem einzigen Stück – sie ist ein sorgfältig konstruierter Stapel von Schichten. Die Grundlage ist ein flexibles Basismaterial, typischerweise Polyimid, das für seine Hitzebeständigkeit und Haltbarkeit bekannt ist. Darüber bildet dünne Kupferfolie die Leiterbahnen, während Klebeschichten oder Klebefolien alles zusammenhalten. Eine Schutzhülle schirmt die Schaltkreise ab und stellt sicher, dass sie Biegungen und Umwelteinflüssen standhalten.
- Basisschicht:Polyimid oder Polyester für Flexibilität.
- Dirigent:Kupfer, geätzt in präzise Muster.
- Deckschicht:Eine Schutzfolie, oft auf Polyimidbasis.
- Klebstoffe:Optional, zum sicheren Verkleben von Schichten.
Wie funktionieren flexible Leiterplatten?
Flexible Leiterplatten funktionieren, indem sie elektrische Signale durch dünne Kupferleiterbahnen leiten, die in ein biegsames Substrat eingebettet sind. Die Magie liegt in ihrer Fähigkeit, die Konnektivität auch dann aufrechtzuerhalten, wenn sie gebogen oder geformt sind. Das Substrat isoliert die Schaltkreise, während das Kupfer für einen effizienten Stromfluss sorgt. Ihr Design ermöglicht es ihnen, dynamische Bewegungen – wie bei einem Klapptelefon – zu bewältigen, ohne zu reißen oder kurzzuschließen, dank der Elastizität des Materials und der präzisen Konstruktion des Materials.
Wo können flexible Leiterplatten eingesetzt werden?
Flexible Leiterplatten glänzen in Branchen, in denen Platz, Gewicht und Anpassungsfähigkeit eine Rolle spielen. In der Unterhaltungselektronik treiben sie Wearables wie Smartwatches und faltbare Bildschirme an. Medizinische Geräte verlassen sich auf sie für kompakte, zuverlässige Sensoren, die sich dem Körper anpassen. In der Luft- und Raumfahrt und im Automobilsektor werden sie in engen, vibrationsintensiven Umgebungen eingesetzt, während die Robotik von ihrer Fähigkeit profitiert, sich nahtlos mit Gelenken und Gliedmaßen zu bewegen.
- Wearables:Fitnesstracker und smarte Kleidung.
- Medizinisch:Implantierbare Geräte und Diagnoseinstrumente.
- Selbstfahrend:Sensoren in geschwungenen Armaturenbrettern.
- Luft- und Raumfahrt:Leichte Verkabelung in Satelliten.
Wie werden flexible Leiterplatten entworfen und hergestellt?
Die Erstellung einer flexiblen Leiterplatte ist eine Mischung aus Präzisionsdesign und fortschrittlicher Fertigung. Es beginnt mit einem Konzept und endet mit einer funktionalen, biegsamen Schaltung. Hier ist ein Schritt-für-Schritt-Blick auf den Prozess:
- Entwurfsphase:Ingenieure verwenden CAD-Software, um das Schaltungslayout abzubilden und so Flexibilität und Platz zu optimieren.
- Materialauswahl:Es wird ein flexibles Substrat wie Polyimid gewählt, gepaart mit Kupfer für die Leitfähigkeit.
- Radierung:Kupfer wird mit Hilfe der Fotolithographie in Muster geätzt, die die Schaltkreise bilden.
- Schichtung:Die Schichten werden unter Hitze und Druck miteinander verbunden.
- Veredelung:Eine Deckschicht wird aufgebracht, und die Platte wird in Form geschnitten, bereit für den Test.
Dieser sorgfältige Prozess stellt sicher, dass das Endprodukt sowohl die Leistungs- als auch die Flexibilitätsanforderungen erfüllt.
Warum werden flexible Leiterplatten gegenüber starren Leiterplatten bevorzugt?
Flexible Leiterplatten zeichnen sich als bahnbrechender Faktor im Elektronikdesign aus und bieten einzigartige Vorteile, die starre Leiterplatten nicht bieten können. Hier sind die Gründe, warum sie oft die erste Wahl sind:
- Anpassungsfähiges Design: Flexible Leiterplatten können sich in engen oder unkonventionellen Räumen biegen und falten und ermöglichen so schlankere, innovativere Produktdesigns wie faltbare Geräte oder winzige medizinische Geräte.
- Verbesserte Ausfallsicherheit: Sie sind so konstruiert, dass sie Vibrationen, Stößen und Biegungen standhalten und starren Leiterplatten in anspruchsvollen Umgebungen wie Fahrzeugen oder Industriemaschinen standhalten.
- Leichte Bauweise: Flexible Leiterplatten bestehen aus dünneren, leichteren Materialien und reduzieren das Gesamtgewicht von Geräten – ein entscheidender Faktor für Wearables, Luft- und Raumfahrt oder Handheld-Technologie.
- Optimierte Montage: Durch den Wegfall vieler Steckverbinder und Kabel vereinfachen sie die Fertigung und erhöhen die Zuverlässigkeit, indem sie Schwachstellen reduzieren.
- Kosteneinsparungen bei der Komplexität: Für komplizierte, mehrschichtige Designs reduzieren flexible Leiterplatten die Produktionsschritte und den Materialbedarf und machen sie für fortschrittliche Anwendungen wirtschaftlich.
Diese Stärken positionieren Flexible PCBs als Top-Wahl für Spitzentechnologie in verschiedenen Branchen.
Welche Umgebungen eignen sich am besten für flexible Leiterplatten?
Flexible Leiterplatten gedeihen unter verschiedenen Bedingungen, aber ihre Leistung hängt davon ab, wie gut ihre Umgebung mit ihren Eigenschaften übereinstimmt. Zu den Schlüsselfaktoren gehören:
- Extreme Temperaturen: Mit Materialien wie Polyimid verarbeiten sie Hitze bis zu 200 °C oder Kälte bis zu -40 °C und eignen sich für Anwendungen von Automotoren bis hin zu Außensensoren.
- Feuchtigkeitsgehalt: Sie widerstehen Feuchtigkeit gut mit Schutzbeschichtungen, aber in nassen Umgebungen wie Meeres- oder tropischen Gebieten ist eine zusätzliche Versiegelung ein Muss.
- Bewegung und Vibration: Perfekt für dynamische Anwendungen – wie Fitness-Tracker oder Robotik – glänzt ihre Flexibilität, obwohl Biegegrenzen eingehalten werden müssen.
- Chemisches Vorhandensein: In Fabriken oder Labors mit ätzenden Substanzen sorgt eine zusätzliche Abschirmung dafür, dass sie im Laufe der Zeit funktionsfähig bleiben.
Die Anpassung ihres Einsatzes an diese Bedingungen erschließt das volle Potenzial flexibler Leiterplatten in realen Szenarien.
Wie testen Hersteller flexible Leiterplatten?
Um sicherzustellen, dass flexible Leiterplatten hohe Standards erfüllen, befolgen die Hersteller einen Schritt-für-Schritt-Testprozess. So wird's gemacht:
- Schritt 1: Oberflächenprüfung: Inspektoren suchen mit fortschrittlichen Vergrößerungswerkzeugen nach Kratzern, falsch ausgerichteten Spuren oder Ätzfehlern.
- Schritt 2: Elektrische Validierung: Kontinuitätsprüfungen bestätigen, dass keine fehlerhaften Pfade vorhanden sind, während Isolationstests Kurzschlüsse erkennen, die die Leistung beeinträchtigen könnten.
- Schritt 3: Biegeprüfung: Boards durchlaufen Tausende von Biegezyklen, um den realen Gebrauch nachzuahmen und sicherzustellen, dass sie unter Belastung nicht reißen.
- Schritt 4: Hitze- und Kälteversuche: Durch thermische Zyklen sind sie Temperaturschwankungen ausgesetzt, was die Stabilität in rauen Klimazonen bestätigt.
- Schritt 5: Festigkeit der Verklebung: Adhäsionstests bestätigen, dass Schichten und Leiterbahnen auch unter Belastung intakt bleiben.
Gemäß Standards wie IPC-6013 stellen diese Methoden sicher, dass jede flexible Leiterplatte für ihre vorgesehene Rolle bereit ist.
Wie wird die Qualität bei der Herstellung flexibler Leiterplatten aufrechterhalten?
Die Herstellung zuverlässiger flexibler Leiterplatten erfordert Präzision in jeder Phase. So wird die Qualität gesichert:
- Erstklassige Materialien: Die Verwendung von langlebigen Polyimidfolien und hochreinem Kupfer sorgt für Flexibilität, ohne die Leitfähigkeit zu beeinträchtigen.
- Präzises Ätzen: Modernste Fotolithografie schafft präzise Schaltkreise und vermeidet Fehler, die die Funktion beeinträchtigen könnten.
- Präzision der Schichten: Bei Multi-Layer-Platinen verhindert eine exakte Ausrichtung Signalprobleme oder elektrische Fehler.
- Automatisierte Scans: Maschinen mit optischer Inspektion fangen winzige Fehler – wie unvollständige Spuren – auf, bevor sie zu Problemen werden.
- Gründliche Endkontrollen: Elektrische, mechanische und Umwelttests bestätigen, dass jede Platine strenge Spezifikationen erfüllt.
Dieser sorgfältige Ansatz liefert flexible Leiterplatten, die unabhängig von der Anwendung eine gleichbleibende Leistung erbringen.
Welche Schritte sollten Sie unternehmen, um flexible Leiterplatten zu schützen?
Flexible Leiterplatten sind zäh, aber die richtige Handhabung hält sie in Topform. Beachten Sie diese Vorsichtsmaßnahmen:
- Biegung begrenzen: Halten Sie sich an den Biegeradius des Herstellers, um Risse in empfindlichen Spuren zu vermeiden.
- Statische Sicherheit: Tragen Sie während der Installation eine antistatische Ausrüstung, um die Komponenten vor ESD-Schäden zu schützen.
- Stabile Montage: Befestigen Sie sie fest, um Biegebelastungen während des Gebrauchs zu vermeiden.
- Hitze Vorsicht: Vermeiden Sie schnelle Temperaturschwankungen, um vor Schichttrennung zu schützen.
- Imprägnierung: Fügen Sie Beschichtungen oder Gehäuse in feuchten Bereichen hinzu, um Feuchtigkeitsschäden zu verhindern.
Diese Schritte stellen sicher, dass flexible Leiterplatten auf lange Sicht zuverlässig und effektiv bleiben.
FAQ
Rezensionen
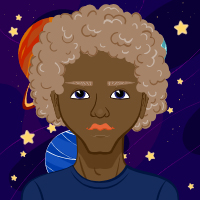
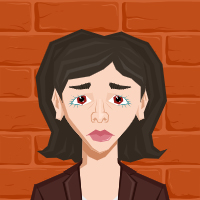
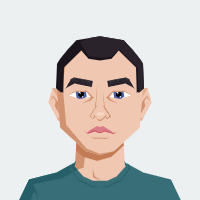
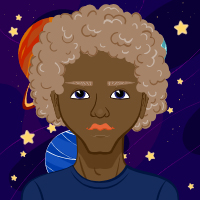

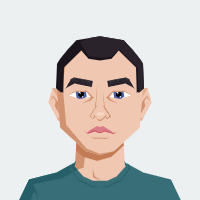
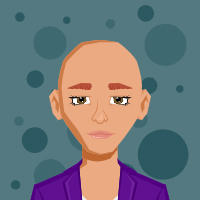
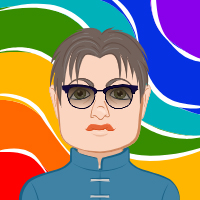
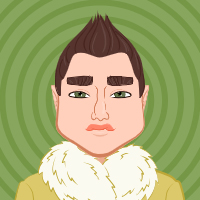
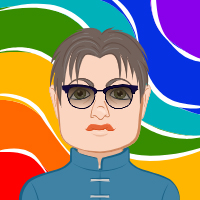